28 May Tips on Surviving an OSHA Visit
Knock, Knock – surprise, it’s OSHA!
What does it take to survive a visit from the Occupational Safety and Health Administration?
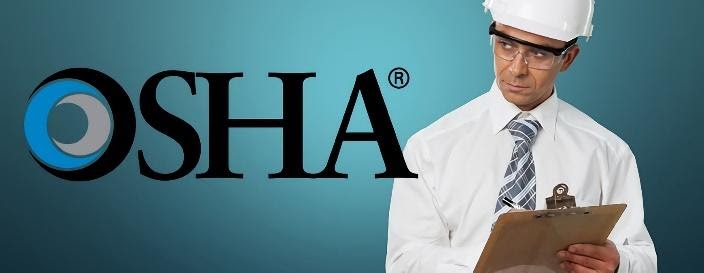
Here are some tips to help keep you in compliance:
- Understand the inspection process
OSHA inspections follow a strict process, starting with the inspector presenting his or her credentials. From there, the inspector explains the purpose of the visit during the opening conference. The inspector will then walk the job site looking for hazards. The process wraps up with the closing conference, where you learn about any violations the inspector found. Knowing the steps can help you explain the process to your employees, which can ease their concerns and help you know what to expect.
- Create an I2P2 (Document every little thing)
A written injury and illness prevention program, known in OSHA-speak as an I2P2, provides a road map for sending employees home injury-free. The plan identifies the hazards employees are exposed to, explains how the company will protect employees and assigns accountability within the program. If you do not have an I2P2 in place, it’s best to be proactive and create one before an injury occurs.
- Keep (very) accurate records
Accurate records are a critical component of any successful safety program and they’re also a key part of OSHA inspections. During the opening conference, you will present your written I2P2, safety training records, medical surveillance records and OSHA logs. The inspector will also ask about applicable OSHA-required programs, such as hazard communication, hearing conservation, forklift safety and confined spaces. This means it’s vital to keep records along the way so that you’re prepared if and when an OSHA inspector comes knocking.
- Don’t interfere with the inspection
Sometimes, an employer allows the inspector to enter but interferes with or limits an important aspect of the inspection, such as the walk-through or employee interviews. Remember that interference could result in legal action. Allow inspectors to see what they are there to inspect, provide them with requested documentation and allow them to speak to employees.
Construction is a high hazard industry that comprises a wide range of activities involving construction, alteration, and/or repair. Construction workers engage in many activities that may expose them to serious hazards, such as falling from rooftops, unguarded machinery, being struck by heavy construction equipment, electrocutions, silica dust, and asbestos.
When it comes to safety and sanitation, OSHA’s constant changes makes ensuring that your construction sites are up to code a cumbersome task. Furthermore, the details and provisions of the regulations differ from state-to-state. The best way to make sure you site is OSHA compliant is to make a habit out of checking for OSHA updates.
Follow the checklist below to identify the major OSHA construction requirements and guidance materials that may apply to your jobsite. These steps will lead you to resources on OSHA’s website that will help you comply with OSHA requirements and prevent workplace injuries and illnesses.
- Step 1: OSHA Requirements Related to Leading Hazards at Construction Sites
- Step 2: Other OSHA Requirements That May Apply to Your Jobsite
- Step 3: Survey Your Workplace for Additional Hazards
- Step 4: Develop a Jobsite Safety and Health Program
- Step 5: Train Your Employees
- Step 6: Recordkeeping, Reporting and Posting
- Step 7: Find Additional Compliance Assistance Information
Sorry, the comment form is closed at this time.